Installation and operation of a spherical tank unit for storing VCM of the CF unit of Bandar Imam Petrochemical Complex
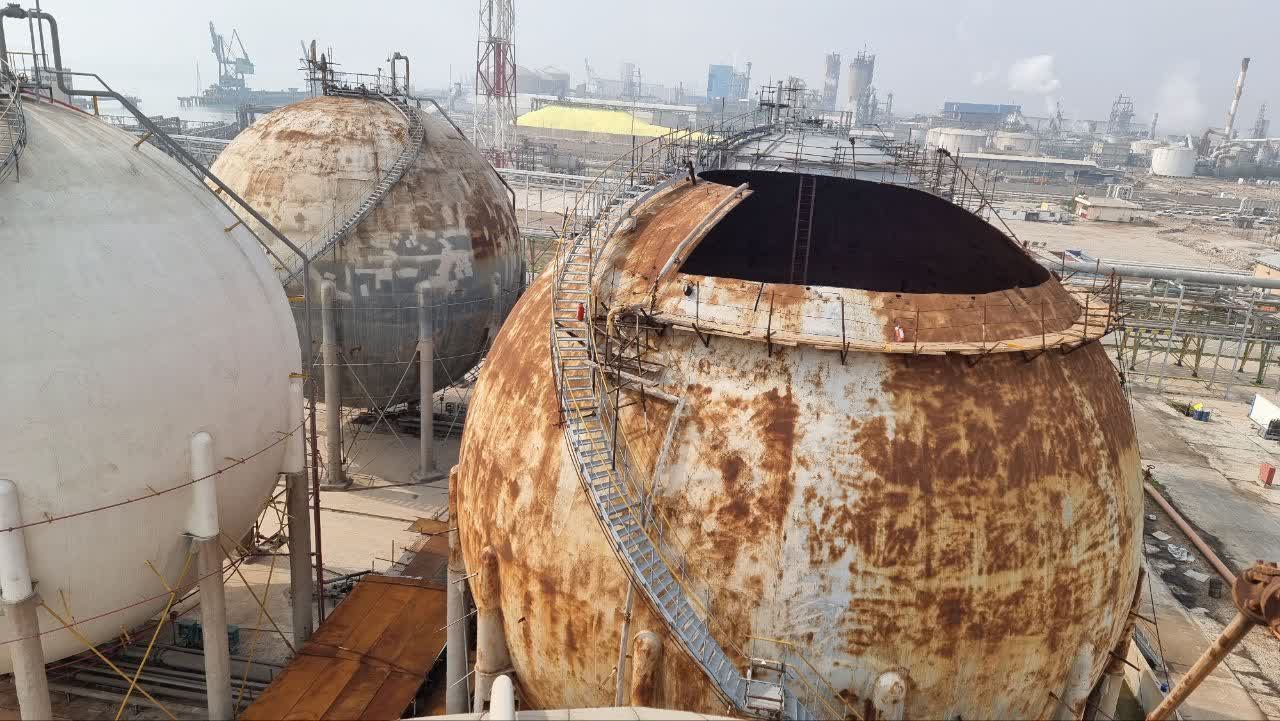
Bandar Imam Petrochemical Company is located in an area of about 270 hectares, on the northwest side of the Persian Gulf in Khuzestan province, 105 km southeast of Ahvaz and 84 km east of Abadan in Mahshahr city
Ease of access to feed, fuel and raw materials, use of road facilities, railway network and sea transportation, the existence of an airport, access to the required water and also help in the development and construction of Khuzestan province as one of the two important poles of industry. Petrochemical in the country and most importantly, creating added value and preventing the burning of oil gases are among the features that justify the choice of this place
Bandaramam Petrochemical Company operates in the field of production of various chemicals, aromatics, polymers and LPG This company is the largest producer of three chains of olefins, aromatics and chlorine akali in Iran
Some of the most important products of this company are; Ethylene, propylene polymer grade, light polyethylene, heavy polyethylene, liquid gas, pentane above, ethane, pyrolysis gasoline, four carbon compounds, caustic soda, ethylene dichloride, vinyl chloride monomer, synthetic rubber, polyvinyl chloride, benzene, A mixture of xylenes, methyl tert-butyl ether and raffinate
Bandaramam Petrochemical is one of the largest and oldest industrial and petrochemical complexes in the country, whose equipment and infrastructure were very complex, old, and wear and tear, and in this regard, the management of the company made a unique move with careful planning in order to protect the production. and protection of national resources and equipment, by accepting possible risks, he took a jihadi and scientific action and started the largest renovation and reconstruction program since the establishment of the company until today with the participation of all managers and employees last year and successfully completed
Bandar Imam Petrochemical carried out these major repairs in three stages, in which 11 units of the company were reconstructed with more than one million man-hours
In these major repairs, replacement and repair of 364 high-risk process lines due to corrosion of 13,800 meters, painting and cold insulation of 15,29 square meters, more than 86,000 welding IDs, 271 heat exchangers, 249 pressure vessels and storage tanks, 39 towers, 42 furnaces and reactors, 1,879 types of safety and industrial valves, 215 types of pumps, 33 compressors and turbines, 1,748 electrical equipments, 86,000 and 632 precision instrument equipments were overhauled using relevant standards and instructions and using internal power
Also, the new 10-inch line from the pressure reduction station was connected next to the 16-inch line, which provided fuel for the power plant and a part of the fuel needed by the boilers, which resulted in significant savings in LPG and diesel consumption
Changing the control system of the Elfin unit from ABB to AV with the most up-to-date control system available in the world, installing 115 Tie-in items to implement very important projects in the field of solving process bottlenecks, such as the use of mixed feed obtained from product development and environmental projects. Carrying out more than 5 thousand square meters of painting chimneys and refractories inside them, repairing and completely dredging the sea water unit of more than 1 thousand and 250 cubic meters of the inlet pond were among the other important measures in this unique overhaul
Looking at a part of the measures taken in these major repairs and realizing the indescribable greatness of this huge movement, one should be proud of the capacity and power of their specialists and compare the performance of the elites and jihadists in the field of production to an industrial miracle